KPI´s, FMEA´s, Six Sigma, Lean Manufacturing
José Joaquín Cabrera Carranco 4-A 19310303
CONTROL ESTADÍSTICO DEL PROCESO, INGENIERÍA DE PROCESOS Y LA RUTA DE LA CALIDAD
El objetivo de cualquier operación de manufactura es encontrar el modo más económico
de hacer productos que cumplan consistentemente con las especificaciones. Esto significa
eliminar el gasto en exceso que resulta de producir productos no utilizables o de realizar
inspecciones innecesarias.
Para cumplir este objetivo, cada persona en una organización debe estar compenetrada
con el progreso y el uso de métodos efectivos. Mediante la introducción de una técnica
probada para mejorar la efectividad de los procesos de manufactura y armando: el control
estadístico de procesos
KPI´s
La planificación y la medición son esenciales para que un negocio tenga éxito. Evaluar cuidadosamente las estrategias y sus resultados permite corregir errores, detectar nuevas oportunidades, anticiparse al comportamiento de los consumidores y tomar mejores decisiones. Para llevar a cabo ese proceso de evaluación continua hay que partir de los indicadores clave de rendimiento.
Indicadores claves de rendimiento: ¿Qué son los KPIs?
Los KPIs (key performance indicator) son indicadores clave de rendimiento que se utilizan para evaluar el éxito de las acciones y/o procesos en la medida en que estos contribuyen a la consecución de los objetivos, para determinar si están dando los frutos esperados o es necesario realizar correcciones.
La importancia de los KPIs
Los indicadores clave de rendimiento permiten medir en tiempo real el funcionamiento de las estrategias de negocios, marketing o ventas brindando una información valiosa para tomar decisiones estratégicas que permitan a la empresa optimizar sus recursos para alcanzar el mejor ROI posible.
Los KPIs también desempeñan una importante función comunicativa ya que informan a directivos, empleados e inversores sobre la evolución de la empresa respecto a los objetivos establecidos, para que todos puedan trabajar con una visión y una meta común.
Ejemplos de KPIs
Ejemplos de performance indicators de una empresa
Cada área del negocio debe tener sus indicadores clave de rendimiento. Los KPIs permiten medir una infinidad de factores, desde el nivel de satisfacción del cliente hasta la calidad de la gestión empresarial o el compromiso de los empleados con la organización.
En el área de ventas, por ejemplo, se puede trabajar con indicadores KPIs como el nivel de facturación, la cuota de mercado, la rentabilidad de cada producto, el número de devoluciones, el índice de fidelización o el ratio entre clientes nuevos y recurrentes. En el área de marketing digital también existen diferentes indicadores clave de rendimiento, desde el número de visitas a la web hasta el alcance orgánico, el engagement, las suscripciones o el coste por conversión.
Lo más importante para determinar los indicadores clave de rendimiento es que correspondan con los objetivos SMART de la organización, de manera que puedan aportar información relevante para optimizar las estrategias empresariales.
FMEA´s
Qué es un análisis FMEA?
La sigla FMEA significa Failure Mode and Effect Analysis o, en español, Análisis Modal de Fallos y Efectos (AMFE). En este contexto, «fallo» significa pérdida de funcionalidad, mientras que «modo de fallo» designa la manera como se produce el fallo. Es una de las herramientas más comunes de análisis de la causa raíz.
Para entender bien la diferencia, veamos un ejemplo sencillo: si un terminal de pago deja de imprimir recibos (fallo identificado) puede ser porque el rollo de papel no está bien colocado (modo de fallo 1) o porque el compartimento no está bien cerrado (modo de fallo 2).
Partiendo de los modos de fallo, podemos llegar a la causa raíz. Sin embargo, el análisis FMEA no se limita a determinar el origen. Esta herramienta se divide en dos partes: primero, la identificación de los modos de fallo (y, por extensión, la posible causa raíz) y luego la evaluación del efecto de ese mismo fallo.
Para entender esta última parte, veamos un ejemplo un poco más complejo. Imagine que una máquina se estropea (fallo) porque el ventilador estaba funcionando con muchas vibraciones (modo de fallo). ¿Qué sucede si se produce este modo de fallo? El equipo se detiene momentáneamente (efecto del fallo), lo que causa pérdidas en la producción.
Diferentes modos de fallo pueden tener diferentes efectos, con consecuencias muy diferentes para el funcionamiento de la empresa. Es por eso que la FMEA a menudo trabaja en conjunto con el análisis de criticidad de activos. Cuando ambos análisis se realizan al mismo tiempo, el resultado se conoce como FMECA, que significa Failure Modes, Effects and Criticality Analysis (Análisis de Modos de Fallo, Efectos y Criticidad).
¿Cuáles son las principales aplicaciones del análisis FMEA?
Y ahora, un poco de historia. El análisis FMEA o AMFE fue desarrollado por el ejército norteamericano en los años 50. Poco después fue adoptado por la industria de la aviación y la NASA, incluyendo en las misiones Apolo, en el desarrollo de las dos sondas Viking y en las misiones interestelares Voyager. La industria del automóvil y la industria petrolera son otros sectores donde el FMEA es habitual.
El análisis FMEA puede ser funcional (centrado en la funcionalidad total del sistema), de procesos (centrado en el análisis de los procesos de producción y montaje) o realizado aún en la fase de diseño/proyecto (principalmente para la gestión de riesgos). Se recomienda hacer un nuevo análisis siempre que se lance un nuevo producto o haya cambios en el funcionamiento de la empresa – cambios en la producción, nuevos reglamentos, etc.- y cuando el feedback de tus clientes informe de un problema recurrente.
¿Cuáles son las ventajas y beneficios de un análisis FMEA?
El objetivo principal de un análisis FMEA es mejorar la calidad, fiabilidad y seguridad de los activos que estamos explorando. Sin embargo, hay una serie de beneficios derivados del proceso de hacer un FMEA en sí mismo:
Desarrollar un método de trabajo que tenga probabilidades de ser exitoso, seguro y confiable.
Evaluar los modos y mecanismos de fallo y su impacto, para clasificarlos según la gravedad y la probabilidad de que ocurran (especialmente si se hace un FMECA). Esta lista de prioridades aumenta la eficacia de su plan de mantenimiento.
Identificar los puntos de fallo y comprobar la integridad del sistema, cuya seguridad no debe estar comprometida, aunque para garantizarlo sea necesaria la introducción de nuevos modos y medidas de seguridad.
Comprobar el efecto de los cambios y ajustes en los procedimientos adoptados y en el diseño del equipo (por ejemplo, comprobar si se reduce la probabilidad de fallo).
Resolución de fallos más rápida, ya que se describen los modos de fallo y sus causas.
Definir los criterios para las pruebas y comprobaciones que deben incluirse en el plan de mantenimiento preventivo basado en los modos de daño descritos.
¿Cuáles son las limitaciones del análisis FMEA?
Por otro lado, hay algunas debilidades en el análisis FMEA:
No es adecuado para los sistemas en los que los fallos pueden producirse simultáneamente, ya que no muestra la causalidad o la correlación entre diversos fallos.
Como veremos más adelante, los tres factores (grado de gravedad/índice de frecuencia/probabilidad de detección de fallos) tienen el mismo peso para el cálculo del riesgo y, desde esta perspectiva, se trata de un análisis muy simplista.
Es un proceso lento que involucra a muchos profesionales, ya que depende directamente de la experiencia de su equipo para enumerar los diversos modos de fallo.
Necesita una actualización constante, ya que el conocimiento sobre el equipo aumenta con la experiencia y el uso; se pueden descubrir modos de fallo inesperados que no se tuvieron en cuenta en el análisis inicial.
Si no se detecta un posible modo de fallo, se subestimará el índice de riesgo de un equipo en particular. Por otro lado, si es demasiado detallado puede dispersar su atención de problemas críticos y desperdiciar recursos.
¿Cómo hacer un análisis FMEA?
La mayor dificultad para hacer un análisis FMEA es la necesidad de ser exhaustivo en cuanto a los modos de fallo, sus causas y su impacto. Lo más común es organizar toda la información en una tabla, en la que recomendamos incluir 7 columnas, una para cada paso.
1. Definir los modos de fallo
El primer paso en un análisis FMEA es definir los modos de fallo para cada componente partiendo de experiencias anteriores con activos similares.
Los análisis de FMEA y FMECA se utilizan comúnmente en industrias peligrosas donde la seguridad es una prioridad. Sin embargo, para el propósito de este artículo, usaremos como ejemplo un plato mal preparado en un restaurante. El ejemplo es de un modo de fallo muy común: encontrar un pelo en el plato. Nuestro crítico Michelin interno distingue también otros tres posibles modos de fallo: encontrar un insecto en el plato, la falta de sal y la intoxicación por salmonela.
Obviamente, un experto en restaurantes conocería muchos más. Este es el gran riesgo del análisis FMEA: no considerar todos los posibles modos de fallo y, como consecuencia, subestimar el riesgo asociado al activo.
2. Describir el efecto del fallo
El segundo paso del análisis FMEA es describir claramente el efecto del fallo en el sistema, ya que este es el factor que determina su gravedad. Intente ser lo más específico posible al describir el efecto del fallo para calcular su impacto en el paso 3.
¿Cuál es el efecto de nuestro modo de fallo? Inmediatamente, devolver el plato. A la larga, no volver nunca más.
3. Impacto ou grado de gravedad del fallo
El grado de gravedad varía de 1 a 10, dependiendo del impacto del fallo:
1 riesgo nulo: los fallos son casi imperceptibles
2-3 riesgo bajo: los fallos son perceptibles pero tienen pocas consecuencias
4- 6 riesgo moderado: las consecuencias de los fallos son evidentes (incluso para los clientes) y afectan al rendimiento del activo
7- 8 riesgo alto: el funcionamiento del activo está totalmente comprometido, lo que causa una interrupción en el orden del día
9-10 riesgo muy alto/crítico: el activo está totalmente comprometido y hay altos riesgos de seguridad
No sabemos qué opinas, pero para nosotros el activo «plato con un pelo» está totalmente comprometido, con altos riesgos de seguridad e higiene. Lo clasificamos con un 9 (reservamos el 10 para la salmonela).
4. La posible causa del fallo
El mismo modo de fallo puede tener varias causas. Por ejemplo, un ascensor que se detiene entre plantas puede tener un error de configuración o un problema de error eléctrico. Si se enumeran todas las causas potenciales, es más fácil probarlas y corregirlas cuando se produce el modo de fallo.
En nuestro ejemplo, la causa raíz es obvia: los empleados de la cocina no llevan gorro. Si hubiéramos encontrado un insecto en la ensalada, ahí sí, tendríamos varias líneas de investigación: comida mal almacenada, fallo en el lavado, infestaciones, etc.
5. Ocurrencia/ Frecuencia de los fallos
La columna de frecuencia debe dar una indicación de la probabilidad de que ocurra el fallo, de nuevo basada en el historial del activo y equipos similares. Normalmente, el Índice de Frecuencia consiste en una clasificación de 1 a 10, donde 1 representa «nada probable» y 10 «muy probable» o «inevitable».
Basándonos en nuestra experiencia personal, calculamos la frecuencia de nuestro modo de fallo en 2.
6. Cómo detectar el fallo
En esta columna debe proponer medidas sobre cómo detectar el fallo. También debe calcular el Índice de Detección de Fallos – la probabilidad de encontrar el error durante el mantenimiento – donde 1 representa «muy probable» y 10 es «nada probable».
En este caso, la forma de detectar el fallo es hacer una inspección visual del plato antes de llevarlo a la mesa. Pero la inspección visual puede ser bastante defectuosa – por lo que a menudo no nos damos cuenta del fallo hasta demasiado tarde. Así que, sin querer sumergirnos más en las malas experiencias, calculamos la probabilidad de detectar el fallo en 4, «probable».
7. Índice de Riesgo
El índice de riesgo es el producto del índice de gravedad (calculado en el paso 3), el índice de frecuencia (calculado en el paso 5) y el índice de detección (calculado en el paso 6). Cuanto más alto sea el índice de riesgo, mayor será la necesidad de tomar medidas de mejora.
El índice de riesgo de nuestro plato, por lo tanto, sería 9* 2*4=72. Si le hubiéramos dado ese 10 a la salmonela, con la misma frecuencia y la misma probabilidad de detectar el fallo, el índice de riesgo sería 80 – es decir, un fallo con mayor prioridad en el plan de mantenimiento. Ahora, es hora de que el análisis FMEA pase de la hoja de Excel al mundo real.
Six Sigma
La metodología Six Sigma fue un concepto creado en los 80 por Bill Smith. Esta metodología fue creada para reducir la variabilidad para reducir o eliminar los defectos o fallos en la entrega de un producto o servicio al cliente/usuario.
El objetivo de Six Sigma es conseguir detectar 3,4 defectos por millón, es decir, cualquier desperfecto que presente el producto o servicio y que no logre cumplir los requisitos del cliente.
Para entender qué es Six Sigma primero deberíamos entender que es la “variación” y cómo se mide.
Sigma (σ) es una letra griega que es entendida como una unidad estadística de mediación. Esta es utilizada para definir la desviación estándar de una población. Esta desviación estándar nos indica qué tan dispersos están los datos con respecto a la media. Como más desviación estándar, mayor dispersión de los datos.
Por tanto, el nivel sigma corresponde a cuántas desviaciones estándar caben entre los límites de especificación del proceso. Por ejemplo, imaginemos que tenemos que fabricar un “producto” que de diámetro tiene que hacer 16 +/- 1mm. Para determinar si este cumple o no con los requisitos del cliente, deberemos tener un límite de especificación inferior a 15mm y superior a 17mm, con un objetivo de 16mm.
Debemos tener en cuenta que la mayoría de empresas tradicionales se encuentran en un nivel 3 sigma, esto significa que suelen tener un 6’37% de defectos en sus procesos. Lo que se pretende es que empiecen a trabajar con 6 sigma, ya que de esta manera, se podrán reducir los defectos a 3’4%.
El objetivo de Six Sigma es conseguir detectar 3,4 defectos por millón, es decir, cualquier desperfecto que presente el producto o servicio y que no logre cumplir los requisitos del cliente.
Para entender qué es Six Sigma primero deberíamos entender que es la “variación” y cómo se mide.
Sigma (σ) es una letra griega que es entendida como una unidad estadística de mediación. Esta es utilizada para definir la desviación estándar de una población. Esta desviación estándar nos indica qué tan dispersos están los datos con respecto a la media. Como más desviación estándar, mayor dispersión de los datos.
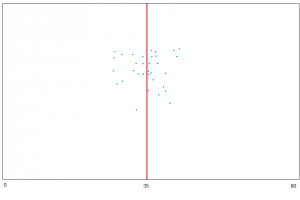
Debemos tener en cuenta que la mayoría de empresas tradicionales se encuentran en un nivel 3 sigma, esto significa que suelen tener un 6’37% de defectos en sus procesos. Lo que se pretende es que empiecen a trabajar con 6 sigma, ya que de esta manera, se podrán reducir los defectos a 3’4%.
Lean Manufacturing
El modelo de gestión Lean Manufacturing tiene como objetivo minimizar las pérdidas y maximizar el valor añadido al cliente. Es un sistema que nació en la industria automovilística y se exportó a todo tipo de empresas. Su éxito en la mejora de la competitividad empresarial demostró que es un valor imprescindible para la supervivencia de las organizaciones. La cuestión es, ¿cuáles son sus principios?
¿Qué es el Lean Manufacturing?
La filosofía Lean Manufacturing, también conocida como Lean Production, es un sistema de organización del trabajo que pone el foco en la mejora del sistema de producción. Para esto se basa en la eliminación de aquellas actividades que no aportan valor al proceso ni al cliente. Estas se denominan despilfarros o desperdicios, y son aquellas tareas que implican la sobreproducción, altos tiempos de espera o desperfectos en los productos, por citar algunos ejemplos.
La filosofía Lean Manufacturing trata de optimizar el sistema de producción y reducir o eliminar las tareas que no añadan valor
El término Lean Manufacturing apareció por primera vez en los años 70 en el libro La máquina que cambió el mundo de los autores Womack, Jones y Ross. La obra, que se ha convertido en best seller mundial, fue la primera que sacó a la luz el sistema de producción lean de Toyota. Este contrapone dos sistemas de negocio radicalmente diferentes: producción lean versus producción en masa.
5 pasos para alcanzar la excelencia Lean
¿Cómo definir una estrategia para la excelencia en servicios? Conoce los pasos clave en el ROADMAP del White Paper LEAN SERVICE de ASENTA y APD y haz que tu compañía despegue.
Dimensión humana de la estrategia
Una de las claves de éxito es su dimensión humana, puesto que las personas son el capital más importante de la empresa. Una cultura empresarial lean implica colaboración y comunicación de todos los niveles de la empresa. Los trabajadores están en contacto permanente con el medio de trabajo, por lo tanto son los primeros en observar y mejorar los problemas. Sin apoyo en las personas del equipo donde haya un clima adecuado, haciéndoles partícipes y comunicando con exactitud lo que se espera de ellos será imposible utilizar las técnicas de mejora de los procesos que propone esta estrategia.
Conceptos clave del Lean Manufacturing
Si tu empresa está interesada en saber más sobre este concepto de estrategia empresarial, debes saber que hay tres aspectos sobre los que bascula la filosofía lean:
Efectividad
Una organización que desarrolla con éxito Lean Manufacturing es una empresa que se enfoca en satisfacer las expectativas del cliente.
Eficiencia
Se utilizan los recursos oportunos, se mejoran los procesos para eliminar aquello que no aporta valor y por lo tanto se alcanza la máxima eficiencia.
Innovación
Una cultura empresarial donde los trabajadores son capaces de identificar los problemas y subsanarlos y que cuenta con un liderazgo comprometido que persigue la mejora constante, es una cultura que apuesta por la innovación.
Conceptos clave del Lean Manufacturing
Filosofía Lean Manufacturing
Son siete los principios que conviene aplicar a una empresa que persigue la filosofía Lean Manufacturing:
1. Hacerlo bien a la primera
Lo que implica conseguir cero defectos. Para ello hay que detectar el problema y solucionarlo desde el origen.
2. Excluir actividades que no añaden valor
Se excluye todo lo que suponga un despilfarro o desperdicio y que no agrega valor añadido a la experiencia de cliente.
3. Mejora continua
Se mantiene la calidad del producto o servicio tratando de reducir costes y aumentar la productividad.
4. Procesos pull
Se produce según demanda puesto que la clave es evitar stocks.
5. Flexibilidad
Es necesario ser capaz de producir diferentes tipos de productos y ajustarse con exactitud a las cantidades.
6. Colaborar con los proveedores
Construir relaciones con los proveedores basándose en el largo plazo, con acuerdos donde compartir riesgo y costes.
7. Cambio de enfoque de venta
Desde el punto de vista Lean Manufacturing, al cliente se le aporta una solución y no un producto o servicio. Esta filosofía tiene que ser única para toda la organización.
Evalúate. Estás cerca de ser una compañía Lean
¿Cómo definir una estrategia para la excelencia en servicios con éxito? Completa el test del White Paper LEAN SERVICE de ASENTA y APD y haz que tu compañía despegue.
Sistemas de producción
Es interesante conocer las diferentes herramientas que son utilizadas en esta estrategia, por lo que vamos a citar cinco sistemas de producción que beben de esta filosofía:
TQM (Total Quality Management): gestión de la calidad total aumentando la eficiencia de la producción y optimizando plazos de entrega.
JIT (Just in time o justo a tiempo): respetar este sistema será producir solo a demanda.
Kaizen: el sistema que asegura la mejora continua.
TOC (Teoría de las restricciones o de las limitaciones): se basa en encontrar el cuello de botella para marcar el ritmo productivo de la cadena.
Reingeniería de procesos: persigue la mejora a gran escala trabajando sobre la redundancia de procesos.
Comentarios
Publicar un comentario